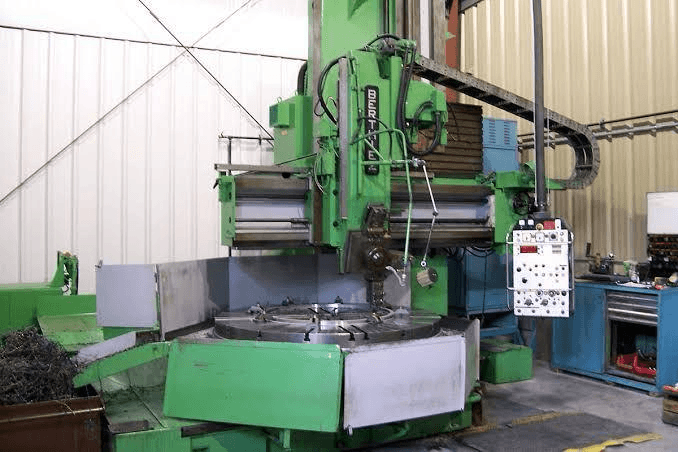
Manufacturing Excellence
State-of-the-art facilities and processes
Our Manufacturing Process
From concept to completion, our comprehensive process ensures quality at every step
Initial Consultation & Design
We work closely with clients to understand their requirements and develop detailed specifications. Our engineering team creates precise 3D models and simulations to optimize the casting design.
Pattern Making & Mold Preparation
High-precision patterns are created based on the approved designs. These patterns are used to form molds with exacting specifications, ensuring dimensional accuracy in the final castings.
Melting & Pouring
Raw materials undergo rigorous quality checks before melting. Our advanced furnaces achieve precise temperature control and chemical composition, verified by spectrometer analysis before pouring.
Heat Treatment & Finishing
Castings undergo specialized heat treatment processes to achieve desired mechanical properties. Final finishing operations include shot blasting, machining, and surface treatments as required.
Quality Assurance & Delivery
Comprehensive testing including dimensional inspection, microstructure analysis, and mechanical property verification ensures every casting meets specifications before careful packaging and delivery.
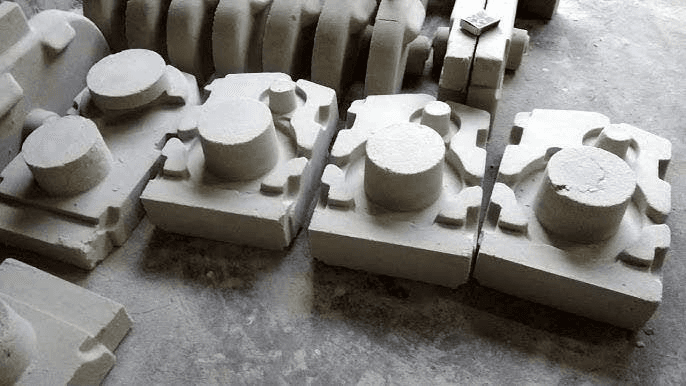
Mould & Core Preparation
Advanced sand mixing and preparation with CO₂ process
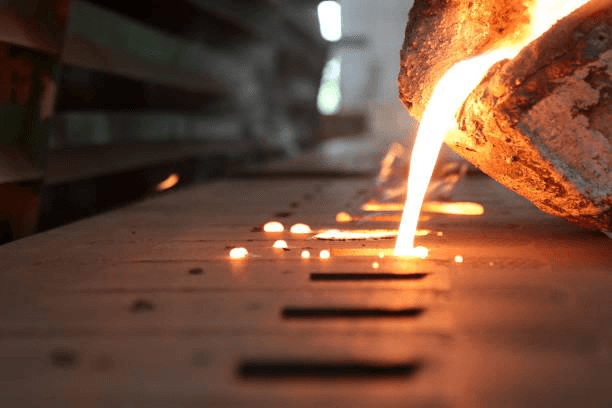
Melting & Pouring
Precision mould making with quality sand and expert craftsmanship
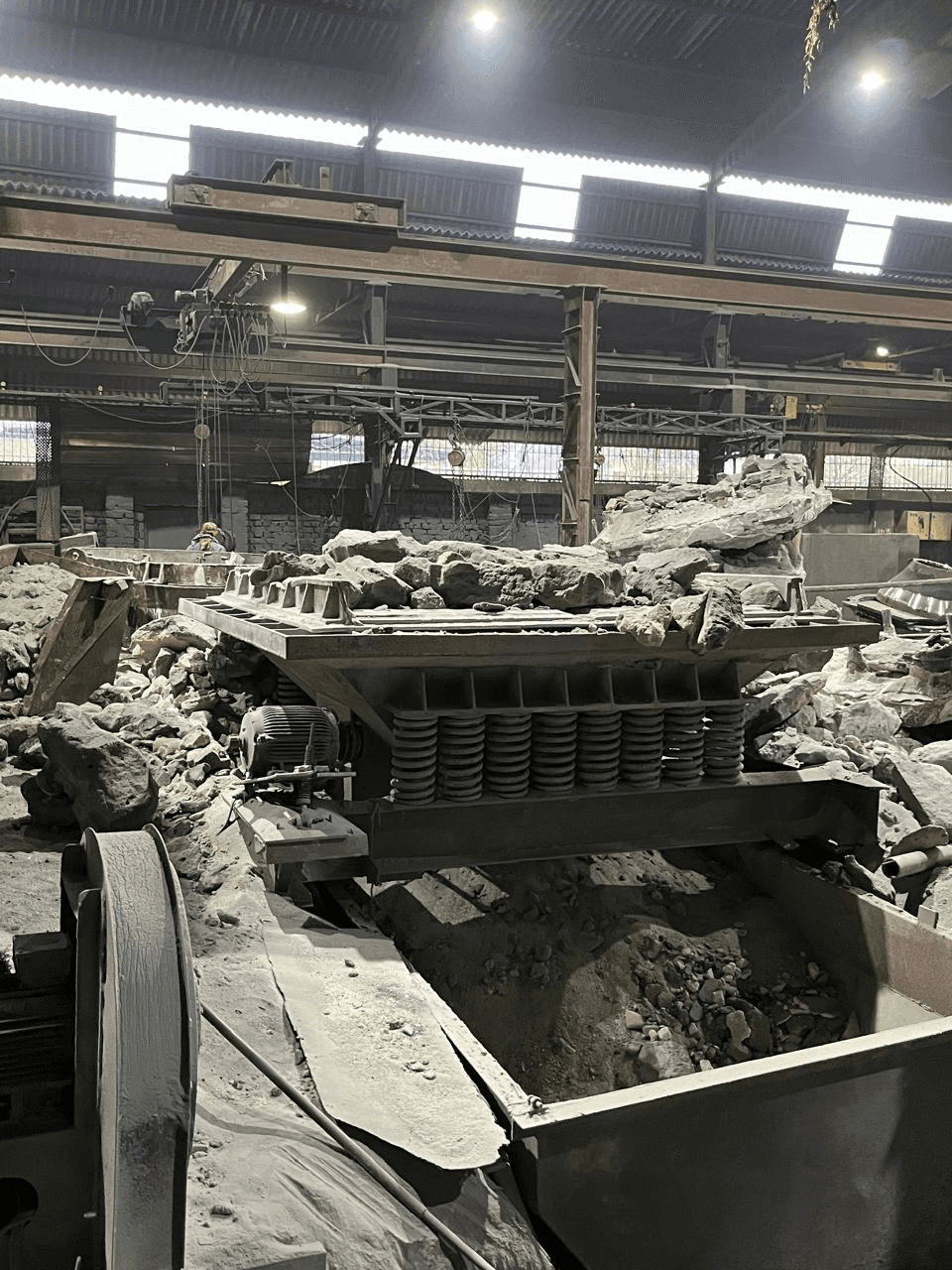
Knockout
Specialized core making for complex internal geometries
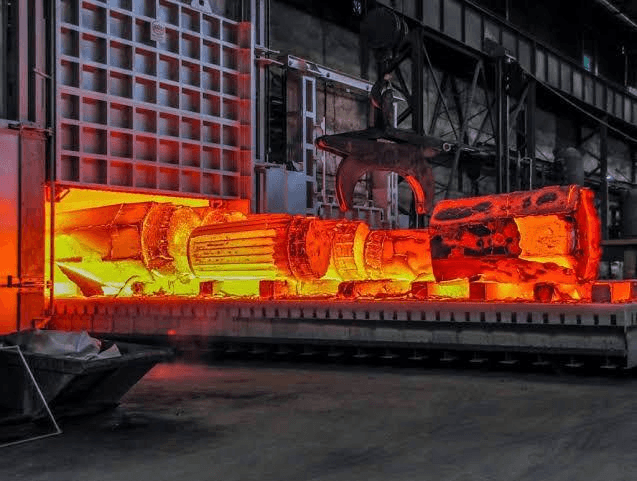
Heat Treatment
Precise cutting of risers and runners followed by quality finishing
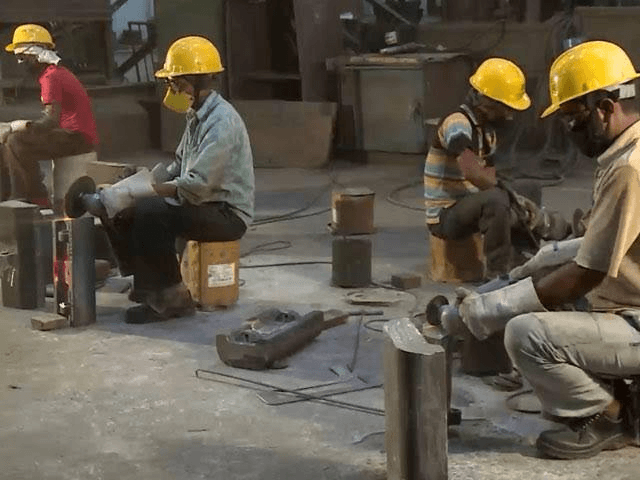
Grinding & Fettling
Environmental-friendly sand recycling and processing
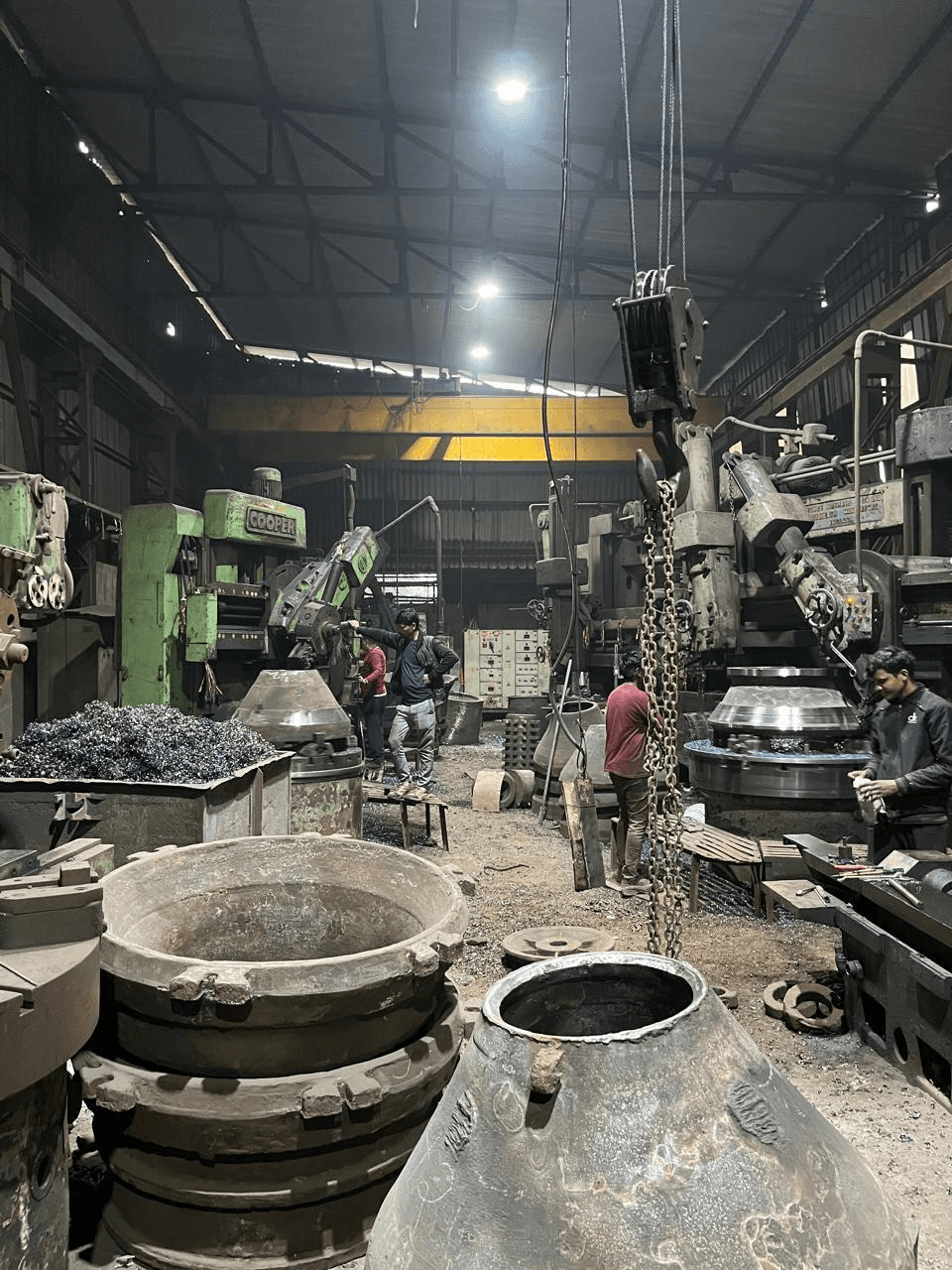
Machining
Rigorous quality control and dimensional verification
Technical Capabilities
melting Equipment
- 1650KVA Induction melting Panel (Inductotherm Make)
- 3 Crucibles (4000Kg, 3000Kg, 1000Kg capacity)
- Laddles of various capacities (250Kg to 4000Kg)
- Laddle heating Systems
- Liquid Metal temperature indicators (Immersion type)
- Bailing machine for scrap handling
moulding Equipment
- Complete CO₂ sand reclamation and handling system
- Super mixer for CO₂ moulding sand with storage hoppers & silos
- Normal sand Muller semi automatic with screw feeding system
- Compaction tables for Semi automated moulding
- CO₂ storage tank with pressure regulation system
- Complete tools for sweep moulding
- All shape and size mould boxes
- Paint mixture machine for homogenizing
infrastructure Equipment
- 1600KVA H.T. Power Connection from DHBVN
- Backup D.G sets (380 KVA and 180 KVA)
- In-house chemical analysis Laboratory
- Dedicated tube well water supply
- 4000 Sq. mtrs. facility on Gurgaon-Alwar Road
- Office Block and Working Shed
- Pattern Shop & Machine Shop
- Transformer Room & Generator Room
heatTreatment Equipment
- 02 Oil Fired furnaces for annealing, normalizing and water quenching
- Large furnace (100'x100'x50') with 05 Thermocouples
- Medium furnace (80'x100'x50') with 04 Thermocouples
- PDI controlled auto cut off heating system
- Online temperature recorder connected to main server
- 5 M.T. fork lift crane with 20'X10'X8' quenching tank
- Air purging and water replenishing system
grindingSection Equipment
- Shot Blasting machine (48' table size)
- 06 Swing Grinders
- 08 Straight Hand Grinders
- 04 Pencil Flexible Grinders
- 04 Surface polishing angle grinders
- Electronic Weigh Bridge (5.0 MT)
- Crane Hanging suspended electronic scale (5 M.T.)
- 04 ARC Welding Sets
- MIG Welding unit
- O2 Manifold system
- 10 LPG Cylinders (19 kg)
machineShop Equipment
- 07 Vertical Turning Lathe Machines (various capacities)
- Double Head Plano miller with Double Bed
- Lathe Machines (20' and 12' Center Height)
- 100 Tonnage Hydraulic Press
- Tool Grinder
- Marking Table (6'x3')
- Bench Type Surface Grinder
Manufacturing Capabilities
State-of-the-art machinery and testing facilities
Machining Center
Machine | Capacity | Qty |
---|---|---|
VTL Machine | 2000x2200x1200 | 01 |
VTL Machine | 1800x2000x1500 | 02 |
VTL Machine | 1600x1600x1200 | 01 |
VTL Machine | 1400x1400x1000 | 02 |
VTL Machine | 1050x1150x1000 | 01 |
Double Head Plano Miller | 8000x3000 | 01 |
Lathe Machine | 20” Center Height | 01 |
Lathe Machine | 12” Center Height | 01 |
Drill Machine | - | 01 |
MNTR Milling Machine | - | 02 |
Hydraulic Press Machine | 100 Ton | 01 |
Testing Facilities
Chemical: 22-channel Spectrometer
Advanced chemical composition analysis
Physical: Rockwell & Poldy Hardness Testing
Comprehensive material strength analysis
NonDestructive: Ultrasonic, MPT
Advanced flaw detection and quality assurance
Pattern Making
woodworking
Bend saw, Hex saw, Drill machine
storage
12 Racks with sliding rollers, 3MT crane
Heat Treatment
furnaces
2 Oil-fired (100'x100'x50' & 80'x100'x50')
controls
PDI controlled, Online temperature recording
quenching
20'x10'x8' tank with air purging system
Infrastructure & Support Facilities
Comprehensive infrastructure supporting our manufacturing excellence
power Supply
- 1600KVA H.T. Power Connection
- 04 Air Compressors with surge tank (10 HP & 15 HP Load)
- Backup D.G sets (380 KVA and 180 KVA)
material Handling
- 10 EOT cranes (2.5 to 15 tonne capacity)
- Electronic and manual weighment scales
- Fork lift crane (5 M.T. capacity)
pattern Shop
- Bend saw
- Flat Hex saw wood cutting machine
- Wooden drill machine
- 12 Rack system with sliding rollers
- 3 M.T. Crane for pattern handling
- Complete pattern repair tooling
office
- Fully furnished office block
- Complete computerization with ERP systems
- Design division with 2D AutoCAD
- SolidWorks for 3D modeling
- Dedicated technical documentation center
Raw Materials & Resources
We maintain strict quality control over our raw materials, sourcing only the finest quality inputs for our casting process.
Primary Materials
Steel Scrap is our main raw material. We source:
- Virgin M.S. CRC scrap from auto ancillary units in NCR
- High-quality old worn out manganese castings spares for secondary scrap
Alloys
High-quality alloying materials including:
- Ferro Manganese
- Silico Manganese
- Ferro Chrome
Consumables
Essential process materials including:
- Quartz sand
- Olivine sand
- Chromite sand
- Zircon Paint
- Thinner
- Graphite Powder
- Grinding wheels
- Welding Electrodes
- Diesel Oil for D.G. set
- Furnace Oil for heat treatment